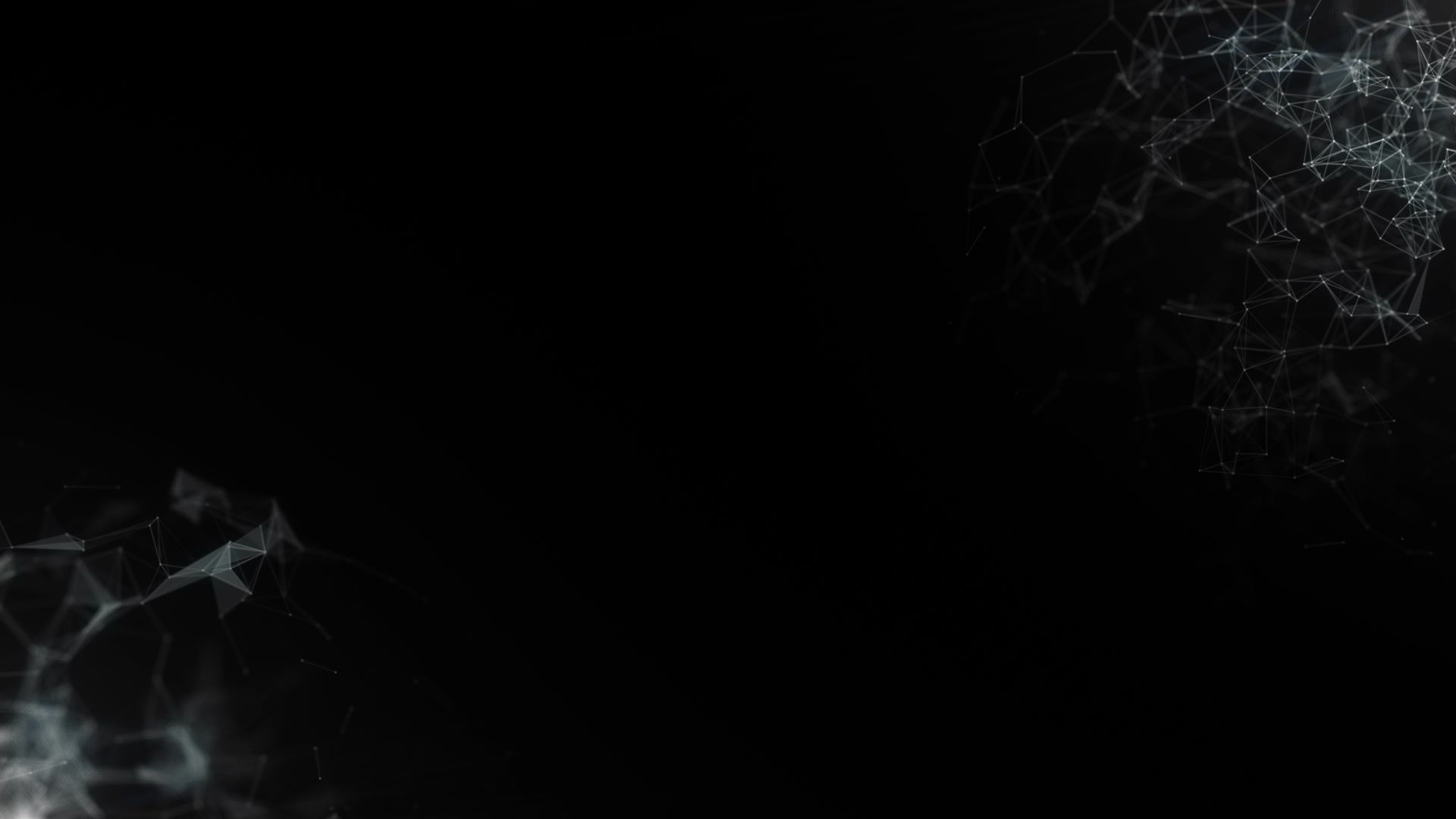
Week 3 Report
Group 5 - Eric Kong, Ayush Kumar, Luna Yang
Week 3 report
Intro and Recap
In the past week, we contacted Dr. Courtney Dunn, Dr. Brad Postier, Dr. Alex R. Carter, Dr. Tychsen, Dr. Ortega, Professor Commean, and Mr. Edouard Trincal to see if any of them would be interested in working with us. A few of the people already had clients, and were therefore unavailable to be our clients. We received a response with Mr. Edouard Trincal (Engineer at BacterioScan) who expressed an interest in working with us, so we scheduled a time to meet with him. Once we learned more about his work and what he wanted from us, we decided to work with Mr. Trincal at BacterioScan. BacterioScan has developed a system to measure bacterial growth in human urine samples. They use a 4-well cuvette to hold individual samples and insert the the cuvettes in the 216Dx device which detects for infection. A manually controlled pressure tester is used to ensure that the cuvettes are not leaking between wells and are not leaking outside of the container. Bacterioscan is planning to move to a new facility and expand production capabilities by the summer of 2019. The current bottleneck in their production and testing process for the cuvettes is utilizing the pressure tester. Mr. Trincal expressed his desires to make the pressure tester more efficient and automated.
Problem: The current pressure tester used by Bacterioscan can only test one cuvette at a time, and the company produces 500 in the course of a week. The design with the clamp is not very ergonomic as many workers complain soreness of the hand after multiple repetitions of closing the air outlet on top of the cuvette. Furthermore, the current software used to collect the data of the pressure test results are unreliable and tend to store excess information.
Goal: In order to improve the efficiency of the pressure tester, we intend to design a new pressure tester that can hold either 4-well or 8-well cuvettes, and the pressure tester should be developed to become automated, instead of the current setup that needs to be manually controlled.
The current setup of the tester is shown in Figure 1.
Figure 1. Current setup of the pressure tester. The blue circle indicates the current setup of clamping the air outlet to the cuvettes. The CTS (shown in red circle) controls the pressure and initiate the test, and the cuvettes were put in the fixture. The screen of the CTS will show whether the cuvette has passed the pressure test.
Figure 2. The figure above shows the views of the current cuvettes that are designed. They can hold up to 4 samples, and the bottom portion of the cuvette with the 4 windows allows for the 261Dx device to emit and absorb light to determine the presence of any bacterial growth.
Client Requests:
During our meeting with Edouard, we compiled a list of important features for the pressure tester that he would like to see in the final product
-
An automatic system that simply required inserting the cuvette and the machine automatically testing its integrity
-
If developing an automatic system is difficult, make the clamp more ergonomic
-
-
The device should fit on the current table (2 ft x 5 ft)
-
The software that collects the data regarding the integrity of each cuvette stores relevant and reliable data.
-
This includes the cuvette number, the reason for failure, and a time stamp
-
-
The machine, software, and CTS should all be compatible with one another
How to solve problem:
On the hardware side of things, we will look into robotics and potential uses that it may provide for this problem. We will have to consider what options are available to us given our budget, but an engineering matrix will be helpful in identifying those in the future. On the software side, there are different programs that can utilize robotic and CTS codes and we have to identify the pros and cons for each.
Future plans:
-
Do research about pressure testing systems. This will include identifying the major systems that already exist and related patent searches
-
Get a better understanding of the process flow within the company and how we can improve the current bottleneck which is the cuvette tester.
-
Begin laying out the problem and all the necessary specs that constrain our contributions
-
To meet with Mr. Trincal in the next week, and discuss a more specific plan of the design. Figure out the materials/equipments/funds that we will need, and set up regular meetings.

