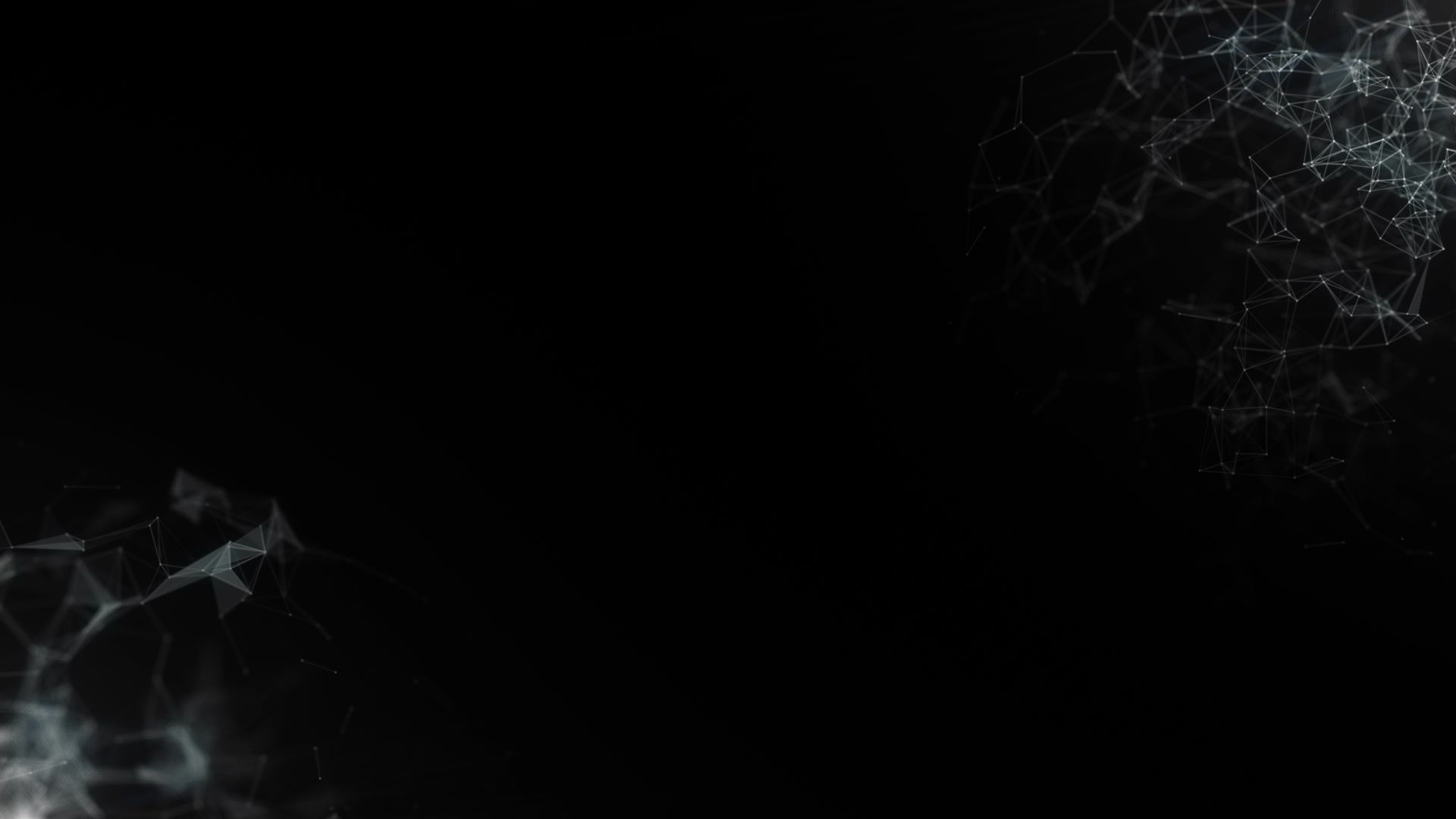
Due to the high demand and many practical applications of leak and pressure testing, there are many existing solutions that have been implemented. One such method, air decay pressure testing, is one of the most commonly used methods for leak testing. It is performed by applying a pressure gradient between the area of interest and the area’s exterior. The pressure decay test utilizes an air tank and transfer it to the testing object until it reaches its target pressure. The rate of pressure decay is measured over a period of time, and the leak of the product can be measured in terms of the loss in pressure. The advantages of using an air decay pressure testing is that the system is sensitive enough to detect small leaks. According to Cincinnati Test Systems, the smallest pressure change that can be detected is recorded at 0.1 Pa, which is equivalent to detecting a volumetric leak of 0.5 cc/min (Sagi, 2001). Additionally, it is a low cost method of identifying leaks compared to other leak testing systems like helium testing.
There are two major kinds of air decay testing, Overpressure air decay testing and Vacuum air decay testing. Overpressure air decay testing can be used at pressures above 0 bar and works for objects with a volume up to 3 liters. The system displays results that are easy to understand and an inexpensive approach. Vacuum air decay testing, on the other hand, needs a vacuum pump to create a low pressure environment (< 0 bar) and is suitable for objects with a volume up to 5 liters.
Air Decay Testing
Water Submersal Dunk Tank
Another method commonly used to detect leaks in complex assemblies using pressure is a dunk tank. This method works by submerging a gas charged part in a tank, allowing the user to detect leaks through a stream of air bubbles escaping from the object of interest. The dunk tank test is useful for showing the path of leaking that could be visualized by tester. However, since it requires visualizing of bubble in order to determine a leak, it is limited and not universally suited for most products. As a result, it is best utilized for detecting large leaks in a container.
Helium Leak Testing
Helium leak testing takes advantage of the fact that helium is both inert and the smallest molecules of all elements. Helium gas it is used as a tracer gas to detect small leaks. A patent for an ultrasensitive helium leak detector was published by Lyle E. Bergquist in 1994 and has since expired. Bergquist invented a leak detector that used helium and argon, taking advantage of their inertness and using them to detect the occurrences of very small leaks. He also introduced a clean momentum transfer type pump with a high compression ratio to for gas evacuation, an entrainment pump to pumps active gases, and used valves and seals to increase the sensitivity in detections of leaks. However, the design Bergquist created had a possibility of absorbing helium into the inner wall of the vacuum chamber. This would interfere with the results of the leak tests, giving inaccurate results. Therefore, another patent was published on January 2nd, 2018 to address this issue. The inventors documented the leak testing system using the accumulated inspection method to reduce the gas from any impurities. They invented a new apparatus to reduce the possibility of the chamber walls absorbing helium gas by changing the steps of the test. They first introduced the gas into the sealed capsule before opening the capsule to release the accumulated leak gas. By doing so, they managed to reduce the likelihood of the chamber walls absorbing the helium.
Leak Testing with Evaporation of Liquid
In this method of testing for leaks in containers, a liquid product is added into the container, sealed, and evacuated to the vapor pressure of the liquid. A vacuum pump is then used to lower the pressure of its surrounding. A pressure monitor is set up outside the container to detect any sudden changes in pressure. If there is a change in pressure, it means that the liquid from the container has evaporated and thus changed the surrounding pressure, which is indicative of a leak. The advantage of this method is its high sensitivity of detecting a change in volume of 0.02 micrometers (Lehmann, 1997). The disadvantage includes the high cost of a vacuum pump and pressure monitor that is sensitive enough to detect small changes in volume. Furthermore, the use of a liquid to test for leaks can result in contaminated containers which poses a problem for testing leaks in cuvettes that need to be sterile before the urine sample is added to ensure its accuracy in identifying UTIs.
Cuvette Belt Faulty Seal Detector
One important aspect of testing that is becoming increasingly important in production lines is automation. While there is a high upfront cost associated with automotive testing, it has long-term economic benefits. Automation can reduce the error and improve efficiency in the production line by avoiding potential human tester error (Ramler and Klaus, et al., 2006). The patent developed by Meguro et. al., 1985 on the cuvette belt details the important aspects of integrating software, hardware, mechanical, and electrical systems to develop an automated system for detecting seal breaks in cuvettes. The automation was developed by utilizing sensors to align the cuvettes with the probe for detecting the seal integrity. The belt system allows multiple cuvettes to be inserted during a single run and then placed in a bin depending on the status of the test. Although this design has a different application from our project, it provides useful information about a strategy we can take when developing a new leak testing system for BacterioScan.